|
DESIGN HISTORY OF H1V8
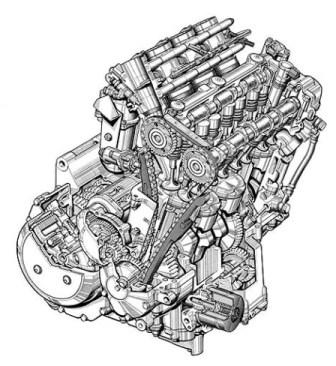 |
 |
The History of the H1V8, the first V8 engine which used mortorcycle head technology from the Suzuki Hayabusa. This is where it all started.
(Note: The H1V8 engine is no longer available and has been replaced by the larger and more powerful H1 MAXI V8.)
Summer of 2002 I decided to build a motorcycle based V8 engine. Sport motorcycle engines were producing remarkable power and the designs had evolved and they now had water cooling and end drive cam drives which made them suitable for a V8 engine. The question was which one. The Suzuki Hayabusa was chosen because it had an end driven camshaft, was the largest displacement and recognized as the most powerful production motorcycle available. Also of interest was the established aftermarket performance parts. This would make performance improvement quick and easy.
A Hayabusa engine was purchased in November 2002, disassembled and the heads and cylinders carefully measured.
|
|
Knowing the size of the heads and cylinders, work began on the general of the layout of the engine. The goal was to make the engine as small as possible. This meant a narrow V angle and short length.
Since the engine would have a flat plan crank, the V angle was open to dimension restrictions only. Inertial calculations were done to confirm that the first order vibration was not too different that the 4 cylinder engine (without the counter rotation balance shaft).
V angles down to 60 degrees were considered, but it quickly was recognized that the separate cylinders and straight intake tracks would eliminate very narrow angles. The decision was really between 75 and 72 degrees. It was decided that 72 degree was too narrow because the metal in the top of the case between the cylinder banks was quickly disappearing as the V got smaller, not leaving much left to hold the top of the case together. A central oil galley is the most compact way to go and it would have been problematic with a 72 deg. angle. So 75 degrees it was going to be.
This proved to be a good decision as the top of the V in the case ended up being very tight with the cylinder skirts, oil jets and crank counter weight all in very close proximity.
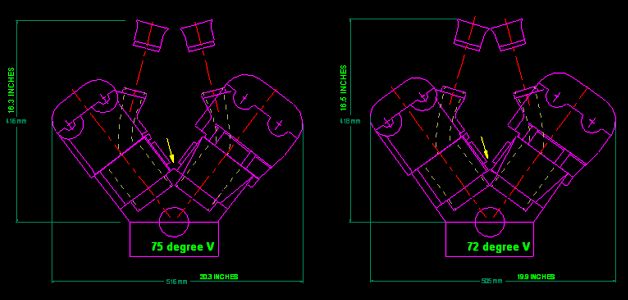
|
 |
|
|
|
 |
Next was the layout of the crank. This is important as it affects the overall length of the engine.
The rods on the left bank (with the reversed head) were offset forward. This allowed the cam chain drive for the right head to occupy the same space as the first rod on the left bank and saves 40mm in the length of the crank and engine. It was a very tight fit and required some clever detail to get it to fit.
The target vehicle was the Caterham 7, and back and forth measurements showed that the engine would easily fit.
In January 2004 a provisional patent was registered. A patent application was submitted a year later and US patent number 7,168,405 was issued in January, 2007.
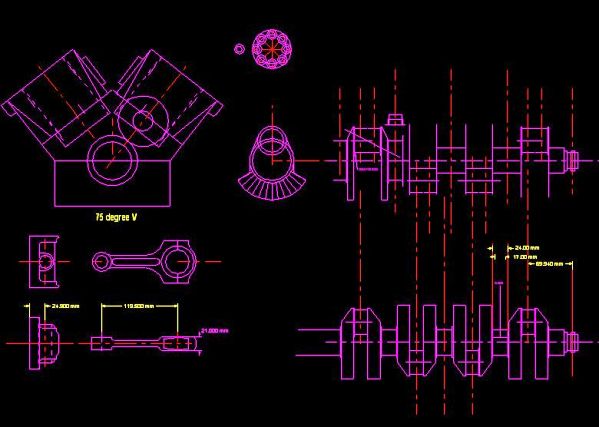
|
|
|
 |
|
|
While we are on the subject of compact size, the below is a picture of a Cosworth xb 2.65 liter Indy engine head next to a Suzuki Hayabusa head came from a website. Using this image, the related separate images of the case of the Cosworth and the case for the H1 engines were properly scaled and attached below and above the heads for comparison. The H1 is on top and the Cosworth on the bottom. With standard bore of 81mm, the H1V8 is 2.6 liters compared to the Cosworth 2.65 liters. The more compact dimensions are accomplished by having much closer cylinder spacing (no wet liners) and a smaller bore/longer stroke. This dramatically shows the compact design inherent in a motorcycle engine design which was retained in the H1 V8 engine. Later versions of the H1V8 were bored and stroked to 84/68 to give a 3 liter displacement with no change to the external size of the engine.
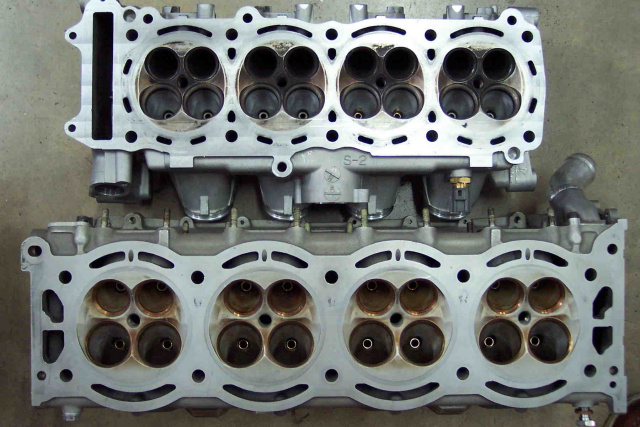
|
 |
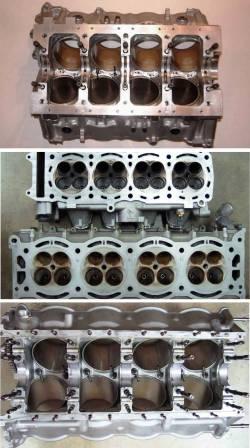 |
|
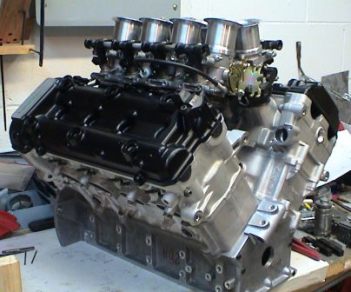 |
 |
The engineering was completed in May 2003 and contracted out in June. The manufacturing cycle of patterns, castings, fixtures, cnc programing and machining parts put the delivery out until December 2003. January a mock up assembly was done to check fit.
Continue to History Page 2...
|
|
|